Instron offers a comprehensive range of fully-integrated dynamic and fatigue testing systems, ranging from 1000 N to 5000 kN. Utilizing servo hydraulic, servo-electric, and linear motor technologies, these testing instruments support a wide variety of fatigue, dynamic, and static testing applications. These include high-cycle fatigue, low-cycle fatigue, thermo-mechanical fatigue, fracture mechanics, crack propagation and growth studies, fracture toughness, bi-axial, axial-torsional, multi-axial testing, high strain rate, quasi-static, creep, stress-relaxation, and many other dynamic and static test types.
Instron's entire range of Dynamic Testing Systems utilizes our state of the art controller the 8800 MT which offers a very high frequency resolution with an exceptional data acquisition rate providing the perfect control for your testing. The controller offers a very low gain setup time without jeopardizing the gain adjustment accuracy. Thanks to our Auto Tuning Feature.
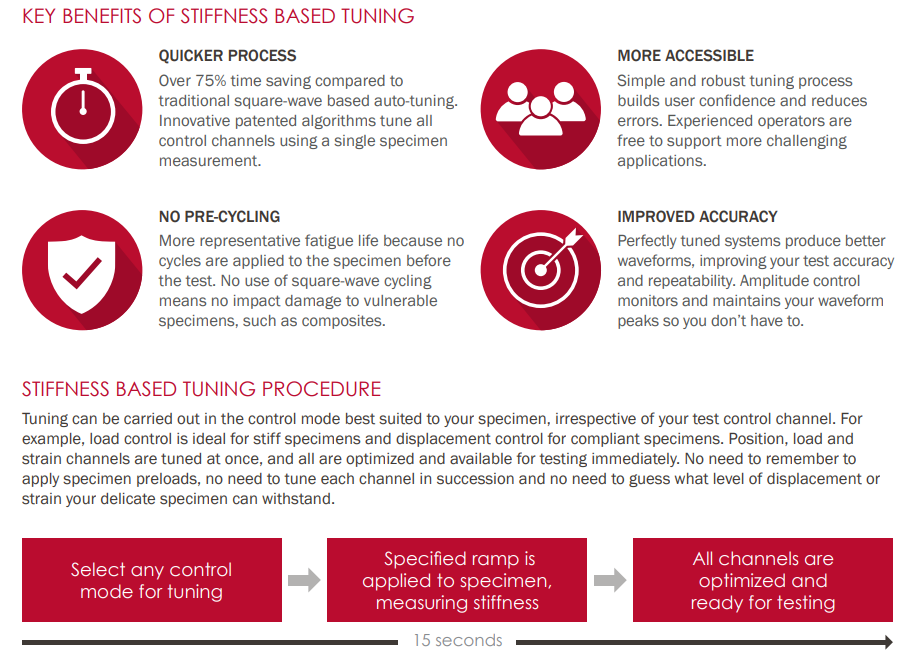
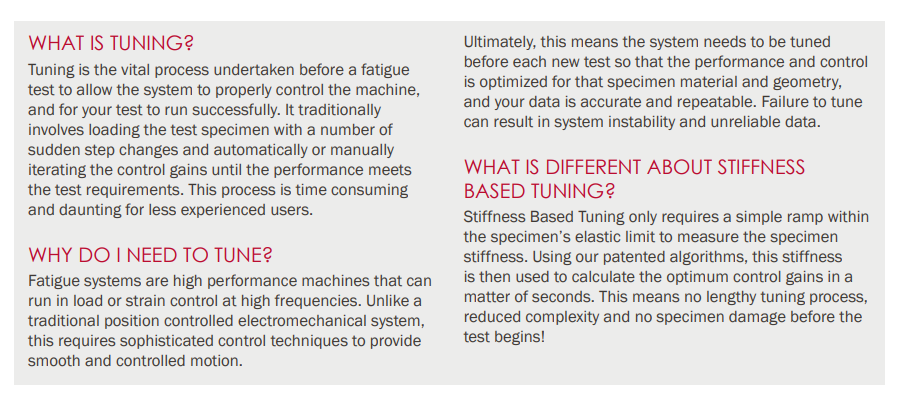
Among our competitors, Instron is the only global materials testing supplier that designs and manufactures its own load cells. This ensures that Instron load cells meet the unique requirements of materials testing such as; high accuracy over a wide measurement range, high stiffness, resistance to offset loads, accurate alignment and excellent zero stability. During tests carried out on dynamic machines, elements of the system are subject to acceleration. As a result, in addition to the force applied to the specimen, the load cell also reads forces resulting from its own movement and the mass of the grips and fixtures attached to it. The accelerometer in a Dynacell™ is right at the heart of the load cell, directly on the load axis. This removes the risk of errors in the acceleration reading resulting from off center loading. This way, the accelerometer is on the load line eliminating both amplitude and phase errors and automatic set-up takes less than one minute.
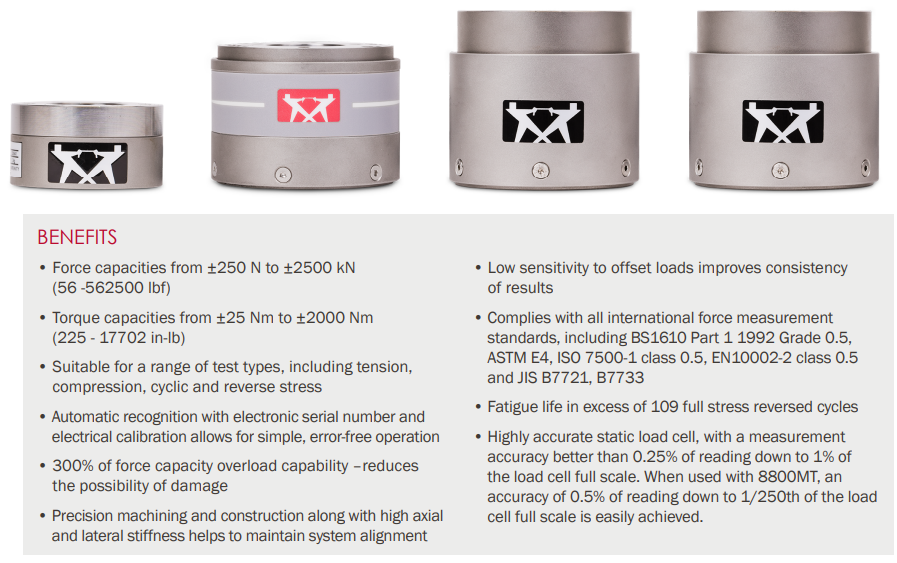
Electropuls Dynamic Testing Range
Instron’s ElectroPuls is a line of high-performance, electrodynamic testing systems designed to perform a wide range of dynamic and static tests on materials and components. Unlike traditional servo-hydraulic systems, ElectroPuls systems use a linear motor technology that operates without oil, eliminating the need for hydraulic infrastructure, making them ideal for labs seeking a cleaner, quieter, and more efficient testing solution.
Key Features of ElectroPuls Systems
- Electrodynamic Actuation: ElectroPuls systems utilize a direct-drive, linear motor, providing high-frequency dynamic performance and precise control for fatigue and static testing. This design allows for a broad testing range without the limitations associated with hydraulic systems.
- Wide Force Range: The ElectroPuls series caters to a broad spectrum of testing needs, with models available from low-force applications (1 kN) to high-force requirements (up to 20 kN). This versatility makes it suitable for testing materials ranging from delicate biomedical specimens to tougher industrial components.
- Clean and Quiet Operation: Since ElectroPuls systems do not require hydraulic fluids or air compressors, they offer a cleaner and quieter operation compared to traditional testing systems. This feature not only reduces maintenance but also creates a safer and more pleasant laboratory environment.
- Advanced Control and Data Acquisition: The ElectroPuls system is equipped with Instron’s advanced control and data acquisition software, Bluehill®, which provides intuitive test setup, real-time data analysis, and enhanced test repeatability. The software’s user-friendly interface simplifies complex testing procedures, enabling more efficient and accurate results.
- High Efficiency and Low Maintenance: With a robust and energy-efficient design, ElectroPuls systems require minimal maintenance. The absence of hydraulic components means fewer wear and tear parts, translating into lower operating costs and reduced downtime.
- Adaptive Testing Capabilities: ElectroPuls systems are adaptable for various testing scenarios, including tension, compression, bend, fatigue, fracture mechanics, and more. Their versatility extends to applications in the biomedical field, such as testing prosthetics, medical implants, and soft tissues.
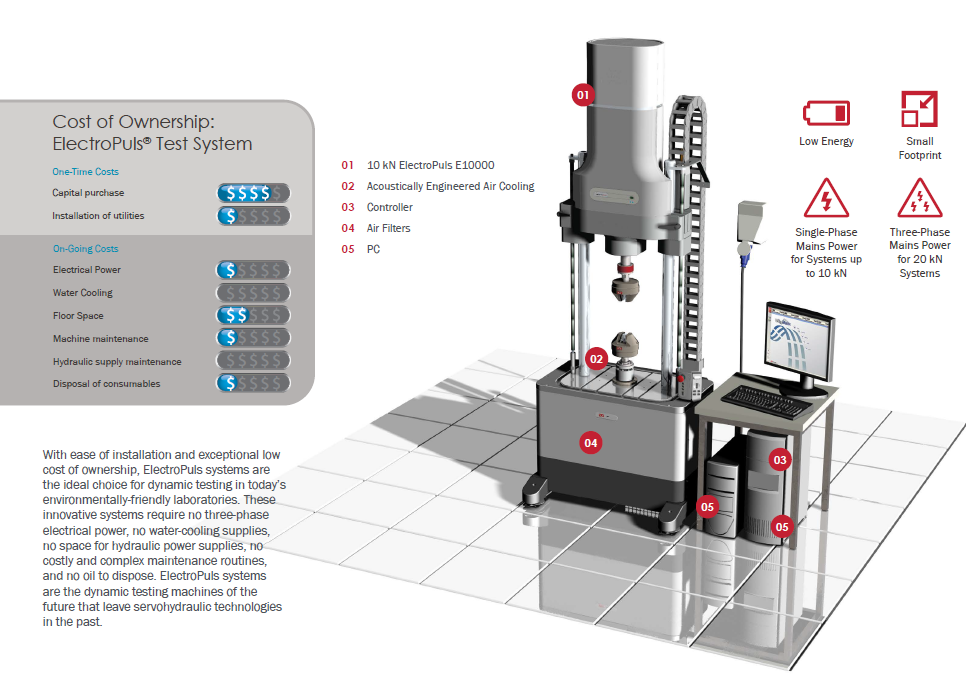
With the presence of our new E20000, you can accurately test your materials using our patented linear motor actuator.
Instron's Servo hydraulic Range of Fatigue testing Systems
Servohydraulic systems are capable of performing an extensive array of tests, including low and high cycle fatigue, crack propagation, fracture toughness, and other dynamic tests. Their ability to generate controlled forces and displacements under varying conditions makes them ideal for simulating real-world loading scenarios. Each system can be customized with the appropriate servo valve, manifold, and hydraulic power unit to suit the specific requirements of any test application, ensuring optimal performance and efficiency.
- Low and High Cycle Fatigue Testing: These tests are critical for evaluating the durability and lifespan of materials and components under cyclic loading conditions. Servohydraulic systems excel in delivering precise cyclic loads, enabling engineers to assess material behavior under repeated stress over thousands or millions of cycles.
- Crack Propagation and Fracture Toughness Testing: Understanding how materials crack and fail under stress is crucial for ensuring safety and reliability in structural applications. Servohydraulic systems provide the precise control needed to evaluate crack initiation and growth, helping to develop materials that can withstand extreme conditions.
- Dynamic Testing Capabilities: Beyond fatigue and fracture testing, servohydraulic systems are used for various dynamic tests, including impact testing, vibration analysis, and more. Their high responsiveness and ability to handle complex loading patterns make them ideal for simulating real-world forces in a controlled laboratory environment.
Advanced Configuration and Customization
Servohydraulic systems offer unmatched flexibility in their configuration. Each system can be readily customized with the appropriate servo valve, manifold, and hydraulic power unit, allowing laboratories to tailor the setup to the specific needs of their application. This adaptability ensures that the system’s performance matches the demands of each test, from low-force biomedical evaluations to high-force structural assessments.
- Servo Valves and Manifolds: Servo valves regulate the flow of hydraulic fluid, controlling the speed and force of the actuator. By selecting the right servo valve size, users can optimize their system for high precision or high-speed testing scenarios. Manifolds ensure the smooth distribution of hydraulic fluid, minimizing pressure drops and maintaining consistent performance.
- Hydraulic Power Units (HPUs): The HPU is the heart of any servohydraulic system, supplying the necessary hydraulic pressure to operate the system. HPUs can be configured to meet the specific requirements of the test setup, ensuring the system delivers the needed power without excessive energy consumption.
Cutting-Edge Control and Software Integration
Instron’s servohydraulic systems are equipped with the advanced 8800MT Controller, Console Software, and Instron’s unique fatigue-rated Dynacell™ load cells, ensuring high precision and control during testing. These components work together to provide accurate force measurements, reliable control feedback, and enhanced safety features.
- 8800MT Controller: This advanced digital controller is designed for high-speed closed-loop control of load, position, and strain, providing precise management of complex test scenarios. Its adaptive algorithms adjust in real-time to changes in specimen behavior, enhancing test accuracy and repeatability.
- Console Software: Console Software offers a comprehensive platform for test control, data acquisition, and analysis. With its intuitive interface, users can easily set up and modify test parameters, monitor real-time data, and generate detailed reports, streamlining the entire testing process.
- Dynacell™ Load Cells: Instron’s Dynacell™ load cells are fatigue-rated and specially designed to withstand the rigorous demands of dynamic testing. They provide high accuracy and reliability in force measurement, reducing the effects of inertia and ensuring that data reflects true material behavior.
- WaveMatrix™3 Dynamic Testing Software: WaveMatrix™3 is the backbone of Instron’s dynamic testing capabilities, providing a powerful platform for designing and running complex dynamic tests. Its flexible waveform generation and real-time control features allow users to simulate a wide range of loading scenarios, from simple sine waves to intricate multi-step tests.
- Application-Specific Software Modules: For specialized testing needs, Instron offers software modules like LCF3 for low cycle fatigue testing and the Fracture Mechanics Suite for standardized fracture tests. These modules provide pre-configured test methods, enhancing efficiency and ensuring compliance with international testing standards.