Polymer Rheology: Melt Flow Testing and Its Importance
Polymer rheology, the study of how polymers flow and deform under various conditions, plays a critical role in understanding the processing and performance of polymer materials. Melt flow testing is a fundamental aspect of polymer rheology, providing valuable insights into the flow characteristics of polymers in their molten state.
Understanding Melt Flow Testing
Melt flow testing evaluates how easily a polymer can be processed when heated to its melting temperature. The flow characteristics measured during this testing are essential for predicting how a polymer will behave during manufacturing processes such as extrusion, injection molding, and blow molding. The results of melt flow testing help manufacturers make informed decisions about material selection, processing conditions, and end-use applications. The two primary parameters measured during melt flow testing are:
- Melt Flow Index (MFI):
The MFI quantifies the flow rate of a polymer through a standardized die under controlled temperature and load conditions. It is expressed in grams per 10 minutes (g/10 min) and provides a direct indication of the polymer’s viscosity and flow characteristics. - Melt Volume Rate (MVR):
The MVR is similar to the MFI but measures the volume of polymer that flows through the die rather than the weight. It is often used for polymers that exhibit significant variability in density and provides a more comprehensive understanding of flow behavior.
Importance of Melt Flow Testing
Melt flow testing is essential for several reasons:
- Processing Optimization:
Understanding the melt flow characteristics of a polymer helps manufacturers optimize processing parameters, ensuring efficient production and minimizing defects in finished products. - Material Characterization:
Melt flow testing provides critical information about a polymer’s molecular weight, molecular weight distribution, and thermal stability, which are essential for predicting performance in specific applications. - Quality Control:
Regular melt flow testing during production helps maintain consistent product quality and performance, enabling manufacturers to detect variations in material properties early in the process.
Standards for Melt Flow Testing
Several international standards govern the methods and procedures for melt flow testing. These standards ensure consistency, accuracy, and reliability in the testing process. The most widely recognized standards include:
- ASTM D1238:
This standard outlines the procedure for determining the melt flow index of thermoplastic resins using a standard method. It specifies the equipment, conditions, and calculations required to accurately measure MFI, providing a comprehensive framework for testing. - ISO 1133:
ISO 1133 is the international standard that corresponds to ASTM D1238. It details the methods for measuring the melt flow rate and melt volume rate of thermoplastics. This standard is crucial for ensuring that test results are comparable across different laboratories and regions. - ASTM D3364:
This standard covers the determination of melt flow rate and melt volume rate for polymers using a capillary rheometer. It provides additional testing methods that can be applied to materials exhibiting non-Newtonian flow behavior, offering a broader perspective on melt rheology. - ISO 11443:
Similar to ASTM D3364, ISO 11443 provides guidelines for measuring the rheological properties of polymers in a molten state using capillary rheometers, allowing for more detailed analysis of flow characteristics under various conditions.
MFi Series: The New Generation of Melt Flow Index Testers
The MFi Series represents the latest advancement in melt flow index testing, designed to perform tests according to ISO 1133 and ASTM D1238 Procedures A, B, and C. This new generation of melt flow testers delivers exceptional performance, combining unparalleled accuracy and reliability with cutting-edge features to meet diverse testing needs.
Key Features and Benefits
- Wide Temperature Range: The MFi Series accommodates a temperature range of up to 450°C, making it suitable for a broad spectrum of thermoplastic materials. This flexibility allows users to conduct melt flow tests on various polymers, ensuring comprehensive material characterization.
- Precision Piston Displacement: With piston displacement accuracy down to 0.02 mm, the MFi Series ensures highly precise measurements of melt flow rates and volumes. This level of accuracy is crucial for obtaining reliable data that can inform processing decisions and product development.
- User-Friendly Interface: Equipped with a capacitive 7” color touchscreen user interface, the MFi Series offers an intuitive experience for operators. The interface simplifies test setup and monitoring, allowing users to navigate through settings and results with ease.
- Efficient Cleaning System: The MFi Series features an easy-to-use cleaning system that minimizes downtime between tests. This capability not only enhances lab efficiency but also reduces the risk of contamination, ensuring that test results remain consistent and accurate.
- Automatic Material Compacting and Purging: To further maximize lab efficiency, the MFi Series incorporates automatic material compacting and purging functions. These features streamline the testing process, reduce manual intervention, and minimize costly errors, allowing laboratories to operate at peak performance.
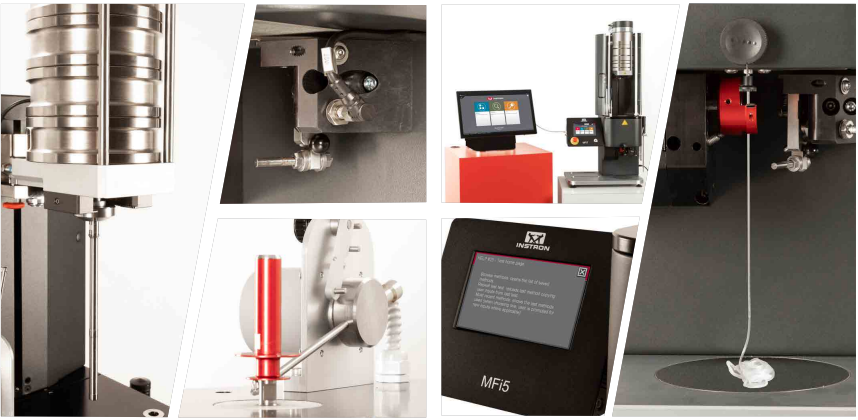
Advantages
- Bluehill® Melt Software: The MFi Series is equipped with Bluehill Melt, featuring easy-to-understand icons and workflows that simplify training and test setup. This intuitive software maximizes lab efficiency while minimizing costly errors, making it accessible even for new operators.
- High Flow Solutions: The light piston and automatic die plug opening facilitate testing of high-flow materials. Different plug tips provide stability and enable the device to work effectively with materials having very high MFR (up to 1600 g/10 min), accommodating a wider range of applications.
- Smart User Interface: Creating a test method requires just three inputs, guided by the Bluehill interface. This streamlined approach reduces the potential for errors, even for inexperienced users. Additionally, operators can view real-time graphs while tests are running, allowing them to monitor MFR/MVR vs. individual measurements, as well as access test results immediately after completion.
- Live Help Feature: The MFi Series includes a Live Help function that provides assistance at any point during the testing process. This feature is designed to reduce the amount of training required for new operators and to prevent costly errors, offering context-sensitive help on each screen as needed.
Models and Available Options
MFi5:
The MFi5 is a quick and reliable basic instrument supplied with a piston travel transducer as standard. It is designed for essential testing needs, with the following optional features available:
- Automatic Die Plug Opening
- Automatic Cutter
- Light piston for high-flow materials
- Corrosion wear-resistant material for barrel, piston, and dies
- UL/CSA version
- Bluehill® Melt Software
MFi7:
The MFi7 is a modular instrument designed for an increasing number of tests. It comes equipped with a piston travel transducer, motorized weightlifter, and emergency stop button as standard. Depending on your testing requirements, the following options are available:
- Automatic Die Plug Opening
- Automatic Cutter
- Light piston for high-flow materials
- Zero Gravity piston
- Safety Shields
- Unit for automatic compacting and purging
- Manual Test Mass Selector
- Corrosion and wear-resistant material for barrel, piston, and dies
CEAST SmartRHEO Series: Advanced Capillary Rheometer Systems
The Instron® capillary rheometer systems of the CEAST SmartRHEO Series are specifically designed for research and development as well as advanced quality control of thermoplastic materials. These systems accurately determine the rheological properties of polymer samples over a wide range of shear rates and testing conditions, making them an essential tool for materials characterization. The CEAST SmartRHEO Series has gained popularity for its compact, robust, and technically advanced instruments, effectively meeting the market demand for reliable testing solutions.
Key Features
- Robust Design: The rigid "H" frame provides high strength and stiffness, ensuring durability and stability during testing. This design is essential for producing consistent and reliable results, even under demanding conditions.
- Precision Movement: The brushless servomotor facilitates accurate piston movement, allowing for precise control over the testing process. This enhances the reliability of the results obtained from each test.
- Advanced Temperature Control: The system features accurate barrel temperature control with three heating zones and multiple PT100 sensors. This setup ensures minimal delay in reaching the desired test temperature and allows for rapid recovery after sample loading, critical for maintaining consistent testing conditions.
- Twin Bore Configuration: The Twin Bore barrel configuration enables two simultaneous and independent rheological tests. This feature allows for direct comparison of the behavior of two different samples or two lots of the same material, significantly increasing efficiency in testing.
- Independent Load Cells: Each piston is equipped with an independent load cell, providing superior accuracy and enhancing the repeatability and reliability of test results. This feature is crucial for obtaining trustworthy data during rheological analysis.
- Accurate Data Acquisition: The system is equipped with two interchangeable and independent barrel-mounted pressure transducers, allowing for precise data acquisition during testing.
- Comprehensive Data Management: Test data are collected, managed, and elaborated by dedicated software, which includes additional modules for deeper rheological data analysis. This capability ensures that users can extract valuable insights from their testing results.
- Versatile Testing Capabilities: A wide selection of optional devices and capillary dies are available, making the CEAST SmartRHEO Series ideal for multiple testing applications within a single machine. This flexibility allows users to expand their testing capabilities as needed.
Range of Models
CEAST SR20:
- Maximum force range of 20 kN.
- Higher capacity for wider characterization.
- Available in single or twin bore barrel configurations.
CEAST SR50:
- Maximum force range of 50 kN.
- Specially reinforced frame for enhanced stability.
- Twin bore barrel configuration for simultaneous testing.